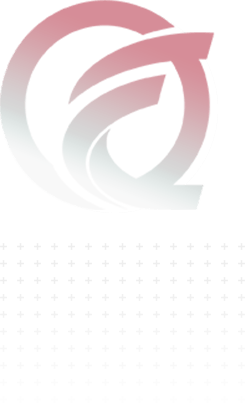
(10)锡林定位、分离罗拉顺转定时(搭接刻度)和钳板闭合定时(钳板开口量)三大工艺参数的配合情况。
在生产实践中,通过调整落棉隔距等工艺参数,能控制精梳机的落棉率,但为降低成本单纯地降低落棉率,往往会对成纱质量造成不利的影响。如果通过精心优化工艺参数,也能轻松实现在保证成纱质量的稳定性的前提下降低1-2个百分点的落棉率。
为解决降低精梳落棉率与保证成纱品质要求的矛盾,我们应该通过提高精梳机的梳理质量,在清除短绒和结杂的同时努力提升精梳条中纤维的伸直度、平行度和分离度,并减小精梳条棉结的尺寸,以降低后工序牵伸过程中产生棉结的可能性,有实际效果的减少成纱棉结。
为探索不同锡林总梳理点对成纱质量的影响,在精梳落棉率相同的条件下,我们在LC70/C30 11.7tex品种上进行了不同总梳理点对成纱质量影响的对比试验,使用原料为70%的长绒棉、30%的细绒棉;试验机型为E65精梳机,车速为350钳次/min,给棉方式为后退给棉。试验结果见表1。
表1 的试验根据结果得出:在落棉率相同的情况下,适当增加锡林齿条的总梳理点,可以有效提升精梳条中纤维的“三度”,由此减少精梳纱的常发性纱疵。
为探索不同锡林齿面角对成纱质量的影响,在精梳落棉率基本相同的条件下,我们分别在8.3tex和5.8tex两个品种上进行了不同齿面角对成纱质量影响的对比试验。
8.3tex品种使用了100%的长绒棉,机型为E62精梳机,车速300 钳次/min,给棉方式后退给棉,试验结果见表2。
表2的试验根据结果得出:落棉率相同的情况下,采用111°齿面角锡林比90°齿面角锡林的成纱IPI疵点减少了19%。
5.8tex采用100%美国长绒棉,机型E65精梳机,车速350钳次/min,小卷定量65克/米;给棉方式后退给棉。试验结果表3。
表3的试验根据结果得出:在落棉率略有增加的情况下,采用111°齿面角锡林,有效提升了锡林总梳理点,提高了精梳条中纤维的三度,减少了后工序在牵伸过程中增加棉结的几率,IPI疵点降低了20%。
(1)在有足够容纤空间的前提下,采用90°齿面角锡林增加适当锡林总梳理点,合理地配置锡林针齿密度,可完全在保证梳理充分的前提下来降低用棉量。
(2)在落棉率基本不变的情况下,采用110°齿面角锡林比90°齿面角锡林的成纱IPI疵点降低10-20%。因此,采用新型加密锡林或者采用111°齿面角的锡林,在保持成纱质量不变的前提下,精梳落棉率可完全下调0.8-1.2个百分点,以降低生产成本。
为探索锡林梳理对成纱质量的影响,我们在JC11.7tex品种上对不同梳理隔距对成纱质量的影响进行了对比试验,使用原料为新疆细绒棉;机型为JSFA588精梳机,速度340钳次/min;锡林型号9030(90°);给棉长度4.7mm,给棉方式前进给棉;小卷定量70g/m。梳理隔距调整前后的对比情况见表4。
适当缩小锡林梳理隔距会使落棉率增加,为此我们重新调整了落棉隔距,将落棉率由18.8%下调到17.7%,做成纱质量试验,结果见表5。
由表5的对比数据可知:适当缩小锡林的梳理隔距,减小了梳理隔距最大值与最小值的差值,接近于等隔距梳理,且最紧点控制在0.20-0.25mm之间,有利于单根纤维化程度的提高,即使在精梳落棉率下调1.1个百分点的情况下,仍然获得较好的成纱质量,在没有新型加密锡林或者111°齿面角的锡林投入的情况下,通过适当缩小锡林的梳理隔距,能够达到既降低了精梳落棉率,又保持了成纱质量稳定性的效果。
缩小锡林梳理隔距,要确保精梳机设备正常运行的安全性,如果调整方法不当,就很容易发生锡林与钳板接针事故。因此要做到以下几点:
(1)在24分度打开上钳板、取出给棉罗拉,用砂纸清洁上下钳唇内嵌塞的异物,在锡林第一排齿片与上钳板钳唇相遇时,必须调整上下钳板完全闭合,标准为0.05mm厚的纸条抽不出,这是确保锡林不接针的基础,很重要。
(2)校正(缩小)锡林梳理隔距前,要检查钳板的开口量,即在24分度用隔距块厚度定位法确定;在29.8分度用4毫米隔距块检查钳板开口量,避免钳板的开口量过大而导致锡林接针。
(4)每次调整落棉隔距时,同时必须要调整钳板的开口量,并且要调整顶梳进出隔距。
(5)规范设备维护润滑操作,严禁油嘴堵塞、油嘴缺失、运动回转部件缺油、机件干磨、锡林轴和下钳板前摆臂的上下轴承磨损,钳板逐渐下沉等,以防止上钳板钳唇与锡林接针。